LES MATIERES PLASTIQUES
CELLULOSIQUES
I ORIGINE
II NITROCELLULOSE
III FABRICATION DE L'ACETATE DE CELLULOSE
IV FABRICATION DES FEUILLES
D'ACETATE
I ORIGINE
a) Introduction
La cellulose est sans doute le matériau le plus répandu
dans le règne végétal, puisque ses fibres constituent
les éléments de tous les arbres et plantes. On l'extrait
à partir de deux sources: Les linters de coton et la pâte
à bois.
b) Cellulose du coton
Les grains de coton fournissent des fibres longues en usage pour le textile
et des fibres courtes ou linters riches en cellulose (90 à 98%).
c) Cellulose du bois
Les pâtes à bois contiennent 55% de cellulose et 30% de lignite
qu'on élimine.
II NITROCELLULOSE
Cellulose + Acide nitrique donnent en présence d'un catalyseur
de la nitrocellulose et de l'eau. Elle est peu utilisée de nos
jours en lunetterie. Elle est inflammable.
III FABRICATION DE L'ACETATE
DE CELLULOSE
Cellulose + Acide Acétique donnent en présence d'un catalyseur
de l'acétate de cellulose et de l'eau.
Dans une cuve, on mélange :
Des solvants: Acide acétique et chlorure de méthylène.
Les catalyseurs: Acide sulfurique et chlorure de zinc.
Les agents d'acétisation: Anhydride acétique.
La réaction dure de 5 à 8 heures. On obtient une masse visqueuse
qui est le triacétate de cellulose. On le traite à l'eau
pour obtenir en précipité l'acétate de cellulose
qui est essoré, séché.
IV FABRICATION DES FEUILLLES D'ACETATE
a) Malaxage
L'acétate séché se présente sous forme de
flocons qui seront malaxés en présence de plastifiants et
de solvants à la température de 60° pendant 3 heures.
Pour 75 kg de flocons d'acétate on ajoute 14 kg de phtalate de
méthyle, 7 kg de phtalate d'éthyle et 7kg de triphényle
de phosphate qui servent de plastifiants. Comme solvants on ajoute 12
kg d'alcool à 95° et 36 kg d'acétone.
b) La pâte obtenue est pressée à 70° au travers
d'une toile métallique fine qui filtre les impuretés solides.
c) Laminage de la pâte se fait sur des laminoirs à écartements
variables, chauffés à 70°. La matière en tournant
entre les cylindres perd une partie de ses solvants. A ce stade, on ajoute
les colorants.
d) Pressage de la pâte jusqu'à la consistance souhaitée.
Elle contient encore 12% de solvants. Elle est alors étirée
sous forme de plaques qui sont empilées et mises sous une presse
à la température de 80° à 95°. Elles se soudent
alors en un seul bloc. Les plaques peuvent être empilées
selon leurs couleurs, parfois recoupées puis à nouveau empilées
pour aboutir à des plaques multicolores et dégradées.
e) Les feuilles obtenues sont placées en étuve à
la température de 40° à 50°. Le reste de solvant
s'élimine alors. Il faut un jour de séchage par millimètre
d'épaisseur.
f) Les feuilles sont plus ou moins déformées à leur
sortie de l'étuve. Elles sont alors redressées à
l'aide de presses hydrauliques où elles sont réchauffées
puis refroidies sous pression.
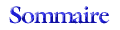 |
|